It was during the final stages of prepping Orion for flight in 2014 when the team discovered a pressing problem: the spacecraft’s thermal barrier seals were recessed below the allowable limit. If these gaps weren’t filled ASAP, Orion would become susceptible to hot plasma gas leaking inside and damaging its systems during the upcoming Exploration Flight 1 (EFT-1) test.
The team needed a solution and needed it quickly.
Luckily, Betty Smith knew just the idea to try. “We can fill the gap,” she told the team, as she busied herself creating a prototype of what would come to be known as the “Betty Barrier.”
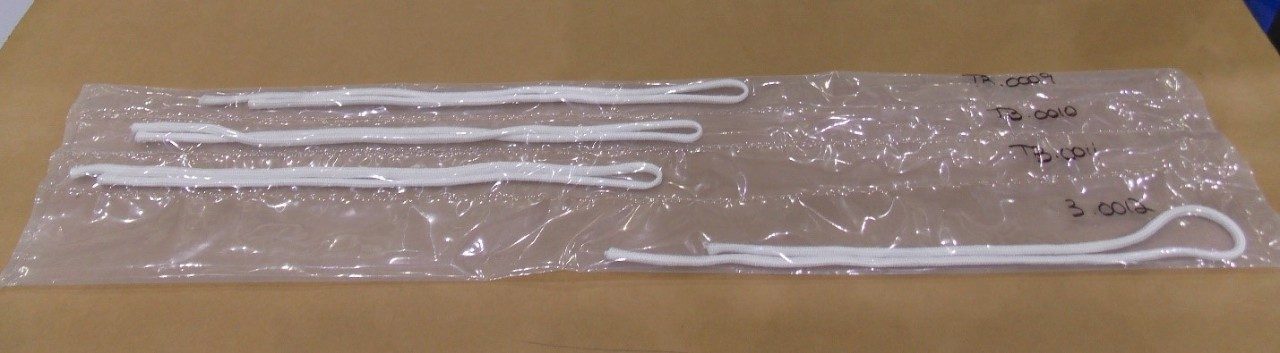
Designing a speedy solution
Betty, who enjoyed working with her hands as a young girl, always knew she wanted a career in the spacecraft business. In 1989, she turned her dream into reality when she began working on the space shuttle program for Rockwell. Betty continued to work on NASA’s space shuttle program for the next two decades, before beginning work at ASRC as a contractor to Lockheed Martin.
“When Lockheed Martin began working on Orion, we hand-selected individuals to bring on board,“ said Jules Schneider, Lockheed Martin’s Orion ATLO director at the Kennedy Space Center. “We chose technicians from the former space shuttle workforce with the specialized skills required to process Orion — skills that don’t exist anywhere else in the world.”
Betty’s former employment came in handy when the thermal protection system (TPS) technician team needed to find a speedy solution to fill the gaps.
“Back then, we were a small group,” Betty recalled. “We talked about it and we made a suggestion based on shuttle experience.”
The team recommended using a hand-sewn sleeve made from fiberglass material and stuffed with fiberglass batting. This would act as a thermal barrier, Betty explained, filling the gap and protecting Orion from airflow penetration. Betty jumped into action, creating and delivering the prototype that same day.
The team saw the barrier supplements were simple to install and posed little risk to the rest of the TPS. The fix worked!
“I just did my job, along with the other technicians,” Betty said. “It wasn’t just me.”
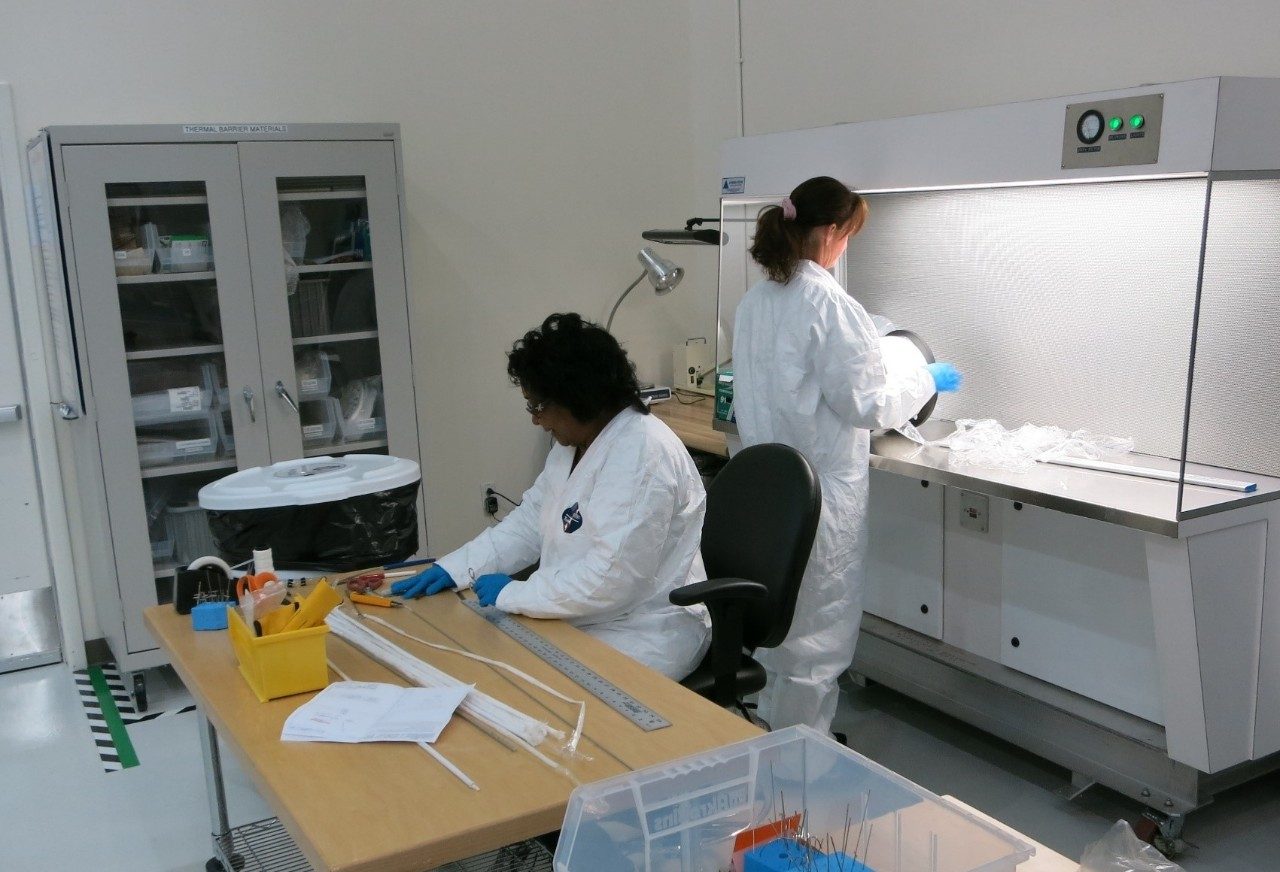
Fulfilling a dream
Fast forward to today, these “Betty Barriers” are now standard flight components, built and stocked alongside other TPS components in order to support a wide range of thermal barrier repairs. The hardware — which will retain its nickname in recognition of its developer — is even referenced multiple places in the Artemis I production schedule, as the team prepares to send the first woman and the next man forward to the Moon.
“I can honestly say I’ve fulfilled my dream,” Betty said. “I like the way my grandsons look at me when they see pictures of what I’ve worked on or come to the site for family day. It makes me feel important.”
Betty — and her impressive barrier fix — will forever be part of the Orion lexicon.
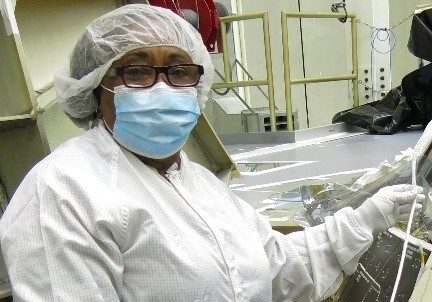