It takes a great team of people and cutting-edge technology and processes to produce the world’s most advanced air defense missile, the PAC-3 Missile Segment Enhancement (MSE). That becomes even more important with increasing demand which is why Lockheed Martin continues to invest in Transformation to make our facilities, processes and world-class team members even more advanced and efficient.
Across our production facilities and Intelligent Factories, we regularly harness the acceleration of business transformation, tech investment and NexGen inspection technology to promote faster and more agile production operations. Evidence of transformation is apparent every day, from our NexGen automated cable and harness technology in Lufkin, Texas, to our world-class machining center in Dallas. We also are investing in a new state-of-the-art missile factory in Camden, Arkansas, that will enable production capacity and cutting-edge All Up Round process capability when it opens later this year.
“The pace of change is energizing and occurring everywhere you look,” said Jason Crager, director of IAMD Production Operations. “Investment in our culture, our facilities, our team member’s ideas and ultimately business process is at the core of our strategy that will enable the trajectory and agility required to support our PAC-3 customers around the world.”
One such example is PAC-3 Development, which leveraged the latest Digital Transformation capabilities in Model Based Circuit Card Assembly (CCA) that resulted in the rapid manufacturing of development products that has allowed the design team to begin hardware checkout and firmware / software integration much sooner in the design process when compared to previous similar efforts.
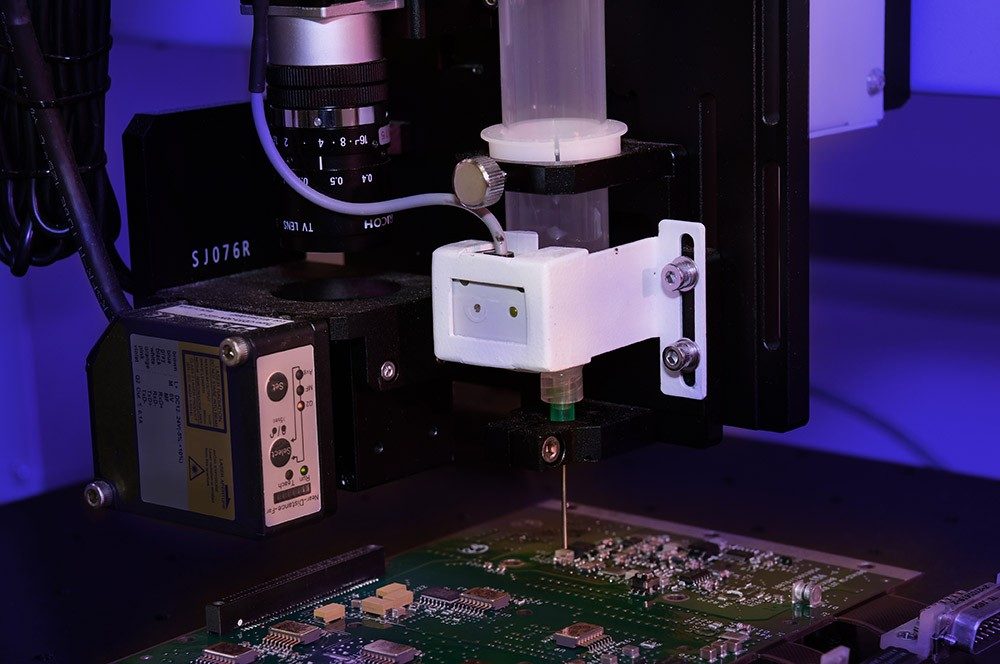
In addition to process improvements like these, we are also investing in and creating a fully automated assembly line for miniaturized microwave components in our Chelmsford, Mass. facility. Coupled with a universal test system, this automated production line will enable rapid assembly and verification of the various radio frequency (RF) micro-electronics that are critical enablers of PAC-3’s proven Hit-To-Kill technology. This important manufacturing evolution will reduce production variation, improve capacity and reduce costs for current products and future designs.
More than 3,125 Lockheed Martin employees support the PAC-3 program in the United States and in countries around the world, including hundreds of Production Operations employees who directly contribute to the PAC-3 MSE being the world’s top interceptor that it is today. This team turns ideas into action and investments that enable agile processes, world-class manufacturing technology and top-tier facilities so we can continue to perform our mission with excellence for our customers.
Currently, 14 countries have chosen the PAC-3 family of interceptors for missile defense, and as the U.S. Government increases its inventory, we continue to see strong demand in East Asia, the Middle East and Europe. As a result, Lockheed Martin has steadily increased production numbers of PAC-3 MSE since achieving a full rate production decision in 2018. Due to increasing demand, Lockheed Martin is advancing funding to increase annual production rates to 550 PAC-3 MSEs by the end of 2024. This is an increase to the original annual production target of 500 PAC-3 MSEs by early 2024.