NASA launched the uncrewed Orion spacecraft out to the Moon and back in 2022 as part of its Artemis I mission. One of the mission’s goals is to test Orion’s heat shield as the spacecraft returns to Earth. Joe Bomba and Damon Erb, two of the engineers leading the heat shield development process, talk about how Lockheed Martin is overcoming the unprecedented challenges the mission faces.
When the Orion crew module speeds through the Earth’s atmosphere to a splashdown in the Pacific Ocean, it will dissipate enough mechanical energy to power 5,000 average U.S. households for a day.
Engineers at Lockheed Martin have created a heat shield and thermal protection system (TPS) tough enough to handle all that energy and heat and safely bring the Orion capsule home, not only for Artemis I in 2022, but also for future crewed flights of NASA’s Artemis lunar exploration program.
“Re-entry is where the heat shield and TPS on the crew module really have to do their job,” says Joe Bomba, Lockheed Martin senior staff aeronautical engineer.
Joe’s job is to analyze aerodynamic loads and aerothermal or air heating environments that the Orion capsule encounters during atmospheric flight – and then find ways to distribute it.
“Spaceflight missions are really all about energy management,” Joe says. “We design the systems required to make those energy transfer processes that are necessary to meet mission objectives possible and efficient, but we also design the vehicle in such a way that – from structures, to subsystem design, to the concept of operations—we minimize or mitigate the environments that are induced from those energy transfer processes.”
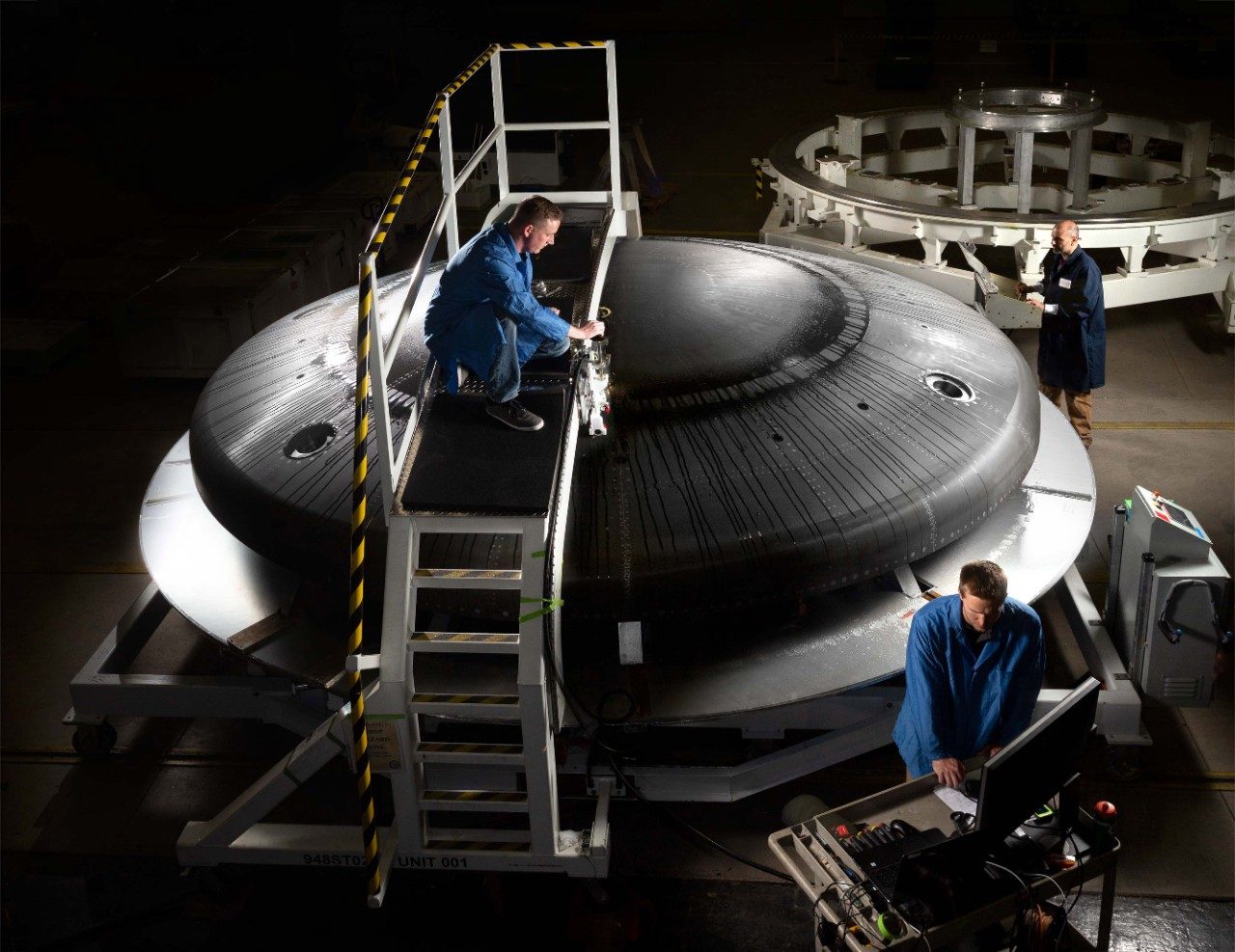
Hotter, Faster, Farther
It’s a big task. A lunar return for Orion will take 24 times longer, travel 1,000 times farther and 7,700 mph faster, and register a temperature 73% hotter – 5,000 degrees Fahrenheit versus 3,000 – compared to a spacecraft returning from low Earth orbit (LEO).
The heat shield’s distinctive shape plays a big role.
“We've leveraged Apollo heritage to derive Orion’s shape, which is very efficient at energy transfer through its blunt shape, which gives us the drag or deceleration we need,” Joe explains. “We also minimize the amount of energy in that transfer that is reabsorbed from the atmosphere to the vehicle.”
That reabsorption percentage is less than 10%, but it’s still an enormous amount of energy. With surface temperatures of the capsule remaining at several thousand degrees, the heat is enough to melt the primary structure that carries the crew. The thermal protection material keeps that from happening. Its design and materials mitigate and accommodate the energy transfer to protect the vehicle.
Building on Apollo
The tried-and-true Apollo heat shield was the basis for Orion’s heat shield, but Orion is designed for deep space exploration not only to the Moon, but to Mars and beyond. Lockheed Martin engineers made some adaptations to make it the safest spacecraft for human exploration ever built.
The heat shield’s TPS still features the same ablative material called AVCOAT used in Apollo missions, but the building process has changed. Instead of having workers fill 300,000 honeycomb cells one by one with ablative material, then heat-cure the material and machine it to the proper shape, the team now manufactures AVCOAT blocks – just fewer than 200 – that are pre-machined to fit into their positions and bonded in place on the heat shield’s carbon fiber skin.
“It’s a huge improvement that lets us build the heat shield structure and the TPS blocks in parallel, instead of waiting for the structure to arrive and start building the TPS,” explains Damon Erb, Lockheed Martin’s heat shield certified principal engineer who oversees design, development, fabrication, testing and installation of the Orion heat shields. “And it makes the process of putting on the AVCOAT substantially quicker – about a quarter of the time.”
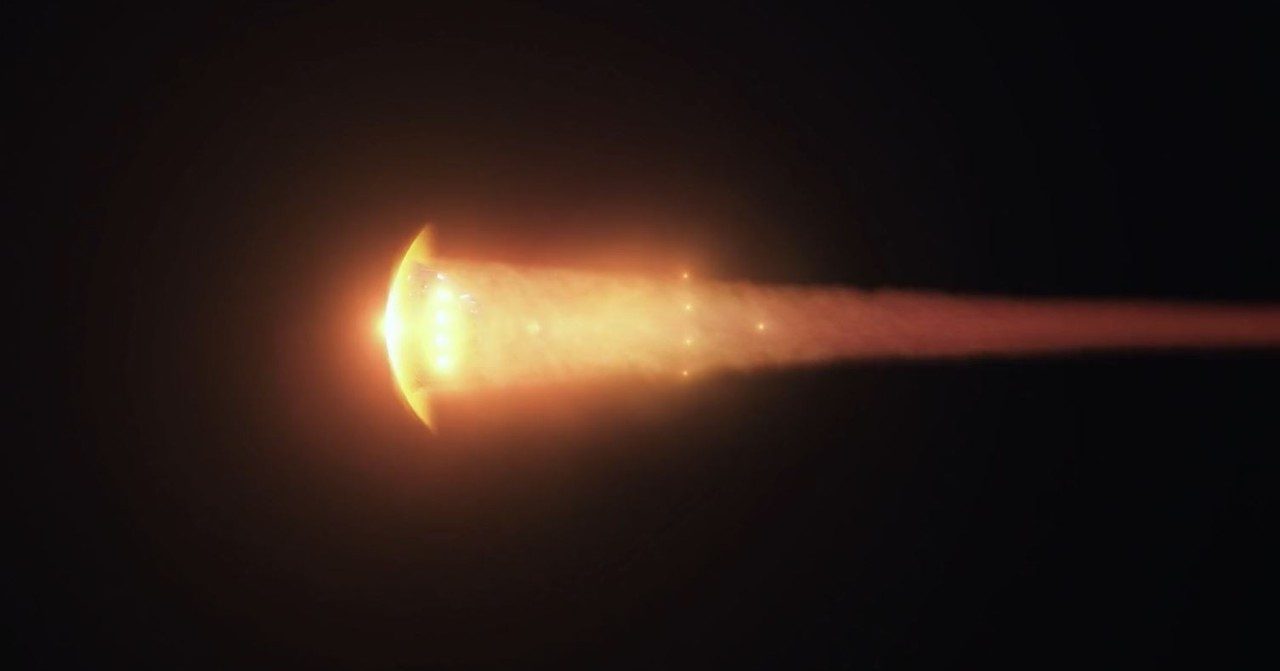
Designed with Mars in Mind
Figuring out the aerothermal environments that are imposed on the heat shield and backshell through re-entry is done through a combination of ground testing and computational fluid dynamics, or CFD, the science that studies the aerodynamic performance of flight vehicles like a spacecraft moving through the atmosphere. It allows for a level of accuracy that ground testing alone can’t provide.
“The ability to perform that level of data analysis, where we are simulating and predicting the flow of hypersonic air over the vehicle and accommodating all the chemistry changes and the radiative environment, that is not a capability that was available in the Apollo era,” Joe says. “And we have leveraged that capability to produce the Orion heat shield with mass minimization in mind.”
The mass minimization was also designed with Mars in mind. “When you come back from Mars, there's a lot more mechanical energy and the entry velocities can be higher than when coming back from the Moon, and considerably higher than from low Earth orbit,” Joe says. “But the design we have today is capable of a return from Mars.”
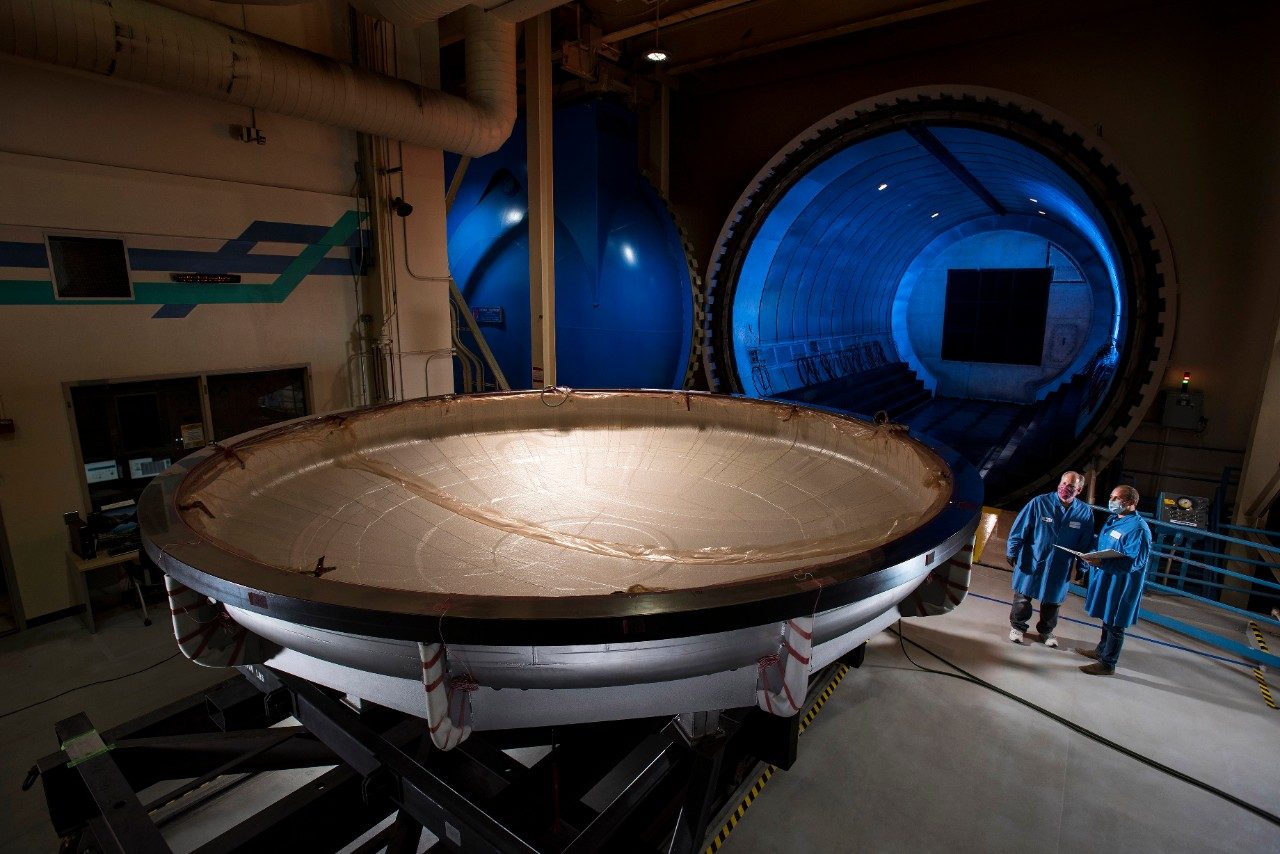
After Artemis I
When the uncrewed Artemis I Orion crew module returns to Earth, Damon, Joe and the team will have more work to do. Because Orion is one of the most heavily instrumented spacecraft ever flown, it will generate an enormous amount of new and useful data on the heat shield’s performance.
“The ground-based testing we do here on Earth can’t simulate the velocities and magnitude of entry heating we will see coming back from the Moon or Mars,” Damon says. “Our entire team is excited to see the results so they can use it to correlate their models back to make sure everything behaves the way we expected.”
The goal is that the structure and TPS is designed to handle future missions with “very minor tweaks,” Damon says.
So far, the team has built three Orion heat shields and is working on two more. For the future, the team plans to move into a steady production rate for future missions. They have already started on the heat shield for Artemis IV.
With the design improvements and the use of digital tools such as augmented reality in manufacturing, “we get better at building every single one,” Damon says. “We are always chasing hard technical problems while also trying to overachieve on cost and schedule. Our heat shields are an example of having the right technical solution in place and making improvements along the way to improve safety, efficiency and cost.”