Leveraging High Energy CT Scan Technology Transformations at Lockheed Martin
You don’t have to be a brain surgeon or oncologist to appreciate the many applications of computed tomography (CT) X-ray scanning. Our engineers at Lockheed Martin Missiles and Fire Control (MFC) have been harnessing and developing advanced applications of this medical technology for decades to take images and analyze product parts during the development and testing phases to ensure our capabilities work the first time, every time.
“Just like a surgeon uses a 3-D CT scan to detect cancer cells within the human body, our Nondestructive Evaluation Lab engineers rely on the power of 3-D/4-D X-ray CT technology to find discontinuities within parts during the development phase, as we rapidly innovate to solve our customers’ most challenging missions,” said Florence Tindle, MFC Vice President of Engineering.
For more than 20 years, Lockheed Martin has partnered with North Star Imaging (NSI) to provide advanced 2-D digital radiography and 3-D/4-D CT imaging and analysis capability within our labs. Most recently, the companies have joined together to develop a high-energy, 9-million-electron-volts (MeV) CT 3-D/4-D scan system – the first breakthrough technology of its kind on the southeastern U.S., just off the Space Coast in Orlando, Florida. For comparison, dental offices typically utilize sixty-to-seventy thousand volts (kV) of low energy X-rays for 2-D digital radiography when discovering discontinuities, like cavities, in teeth.
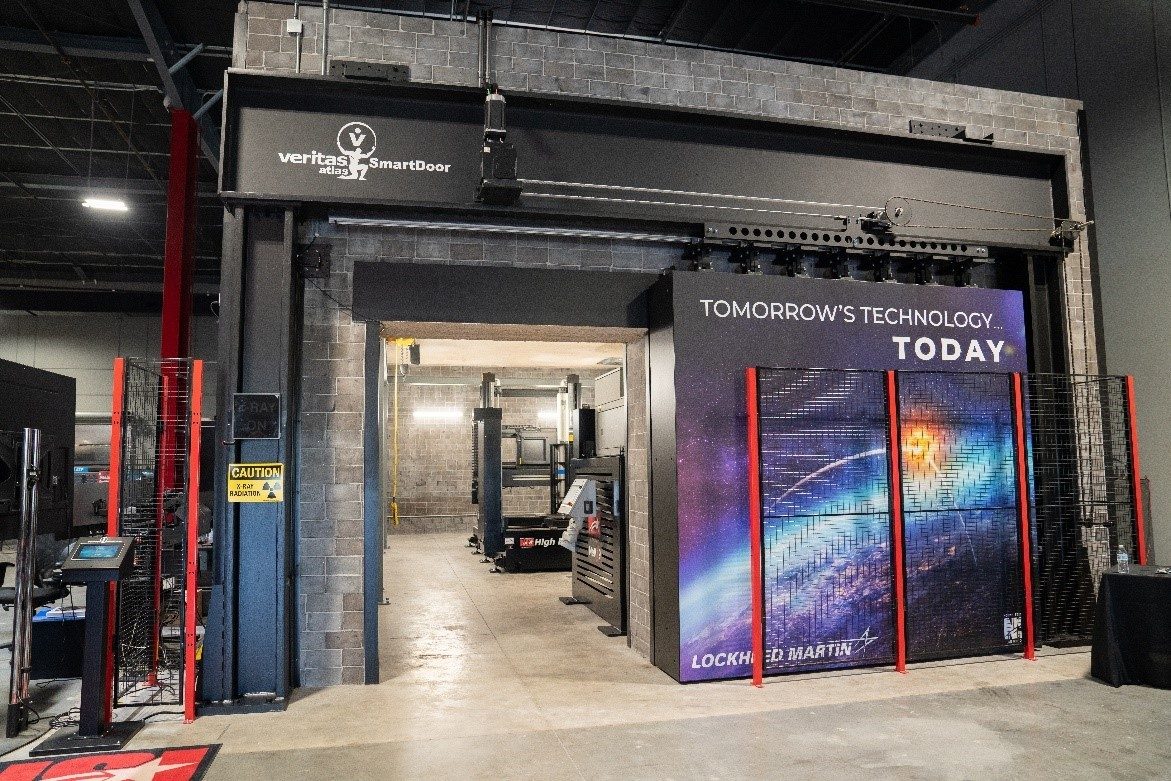
This new, high-energy system is capable of scanning larger and more dense parts – such as 14 inches of steel – than ever before, allowing engineers to see the unseen sooner. The system has multiple X-ray sources and detectors. Additionally, this system can inspect additively manufactured parts as well as energetic material to support Department of Defense (DoD) projects
“With this technology, yesterday’s impossible is today’s opportunity,” said Brett Muehlhauser, Research and Development Technical Fellow at NSI. “We’re able to share this technology capability with the larger aerospace and aviation business community, to provide real-world solutions that are stronger, safer and even more reliable.”
We have already seen a substantial achievement in cost reduction and an increase in throughput for customers regarding complex geometry castings of advanced alloys in the F-35 Electro Optical Targeting System (EOTS), hypersonics products and additively manufactured parts.
As part of the F-35 blueprint for affordability goal, Lockheed Martin’s skilled and dedicated engineers developed new ways to combine materials that form the F-35 EOTS Azimuth Gimbal Housing. This structure in the EOTS Gimbal line replaceable component supports all moving parts. By combining alloys during the casting process, engineers were able to reduce the cost of the Gimbal subassembly. Through CT scanning examination, our engineers could gain insight into the characteristics of the alloy casting process to confirm this innovative solution worked – and shaved time off the development process. The team realized a savings of approximately $25,000 per unit while also paving the way for the SNIPER® Advanced Targeting Pod to follow a similar casting process and cost savings.
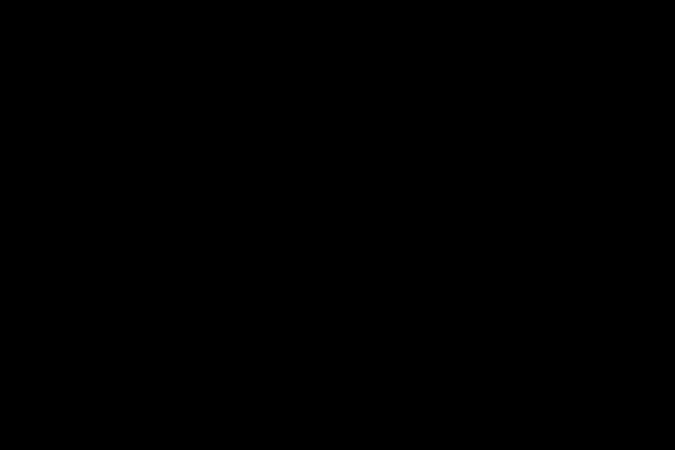
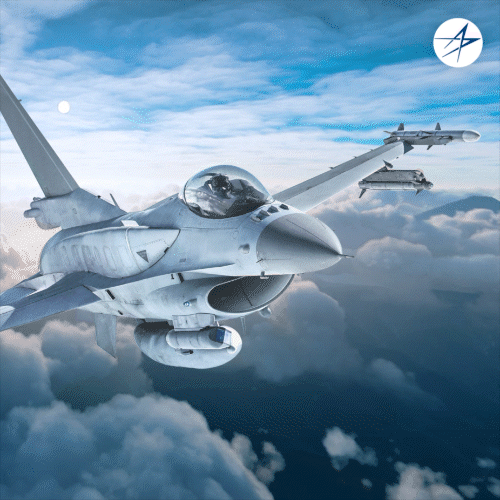
Lockheed Martin engineers identified approaches to further reduce the cost of manufacturing the dependable, mission critical capability of Javelin for our customers. By using CT X-ray technology, the mechanical engineering team developed a new composite fabrication technique that reduced post-machining cost of the Javelin’s launch tube structure. “The CT showed exactly where we needed to make improvements to reduce entrapped voids between the layers of the carbon fiber and at bond joints in our design phase,” said Dickson, an engineer for the initiative. “We always try to find ways where we can improve affordability for our customers and get them our capabilities even more quickly. CT allows us to do just that.”
In 2017, Lockheed Martin engineers strategized ways to rapidly cool 300+ watts of computer thermal power for the TacIRST detector system within an aircraft. CT X-ray technology was one of the major enablers for the engineers to additively manufacture chassis housing the system to solve this challenge. “With the data richness of CT and the digital thread of Computerized-Aided Design (CAD) to additively manufacture this part, we could deploy this high-quality product quickly for our customer,” said Steven, an engineer working the effort. “Our customers were amazed when we showed them our progress and CT scans during the preliminary design review. We’ve cut a three-year development process down to about six months.”
These examples of how our engineers are using high-energy CT are just a few of the many ways we’re utilizing this powerful 3-D/4-D X-ray technology to keep our customers Ahead of Ready. With high-energy CT, the team continues to innovate, maintain and update modern solutions to deliver capabilities quickly when our customers need them most for their rapidly evolving missions.
We’re creating a model-based enterprise with a fully integrated digital thread throughout the design, build and sustainment product lifecycle. Through new innovations and partnerships like NSI and the CT 9MeV X-ray system, we will continue to accelerate transformative technologies and tailored solutions to support our customers’ national security missions.