Not since the introduction of the assembly line has manufacturing experienced revolutionary advancements like those produced by the digital factory. What was once just an ambitious, futuristic concept, the digital factory has become a reality at Lockheed Martin – one that exists in brick and mortar as much as in cloud-based data lakes. Physical and digital worlds have converged in intelligent, flexible factories, or digitally integrated production facilities. There, our teams can better collaborate with customers and industry partners to make how we work as advanced as what we work on, using legacy tools and new best practices to deliver faster and more affordable solutions.
“Lockheed Martin mechanics are true artisans, and they are skilled at building complex products at tight tolerances,” said Mike Sarpu, Lockheed Martin’s vice president of Operations Process Transformation. “We are making investments to augment their craftsmanship in digital factories across the country, giving our production workforce the flexible, intelligent, technology-enabled space they need to support our customers now and well into the future.”
Factory by the Numbers
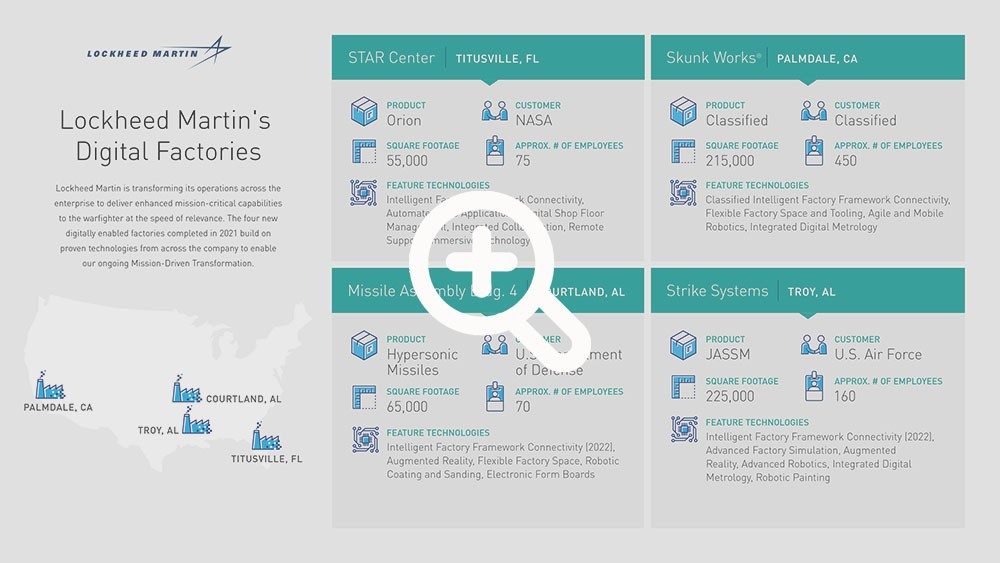
Click to view details about our Digital Factories
Some digital factories have an open floor plan with minimized hard monuments, and are enabled by flexible utility infrastructure, mobile tooling and mobile equipment. Others are dedicated to specific products, such as STAR’s focus on Orion and the MFC factory’s focus on JASSM.
Beyond these four new factories, others are undergoing partial conversions into digitally enabled spaces due to the necessity of preserving the existing program infrastructure. One example is the F-35 Lightning II factory in Fort Worth, Texas. Collectively, the impact of these new and upgraded factories represents Lockheed Martin’s commitment to investing in American manufacturing capabilities for the long term to produce affordable, cutting-edge products at the speed of relevance. Over the next three years, Lockheed Martin plans to invest more than $330 million into new facilities and digital capabilities in existing factories.
Innovative Technologies
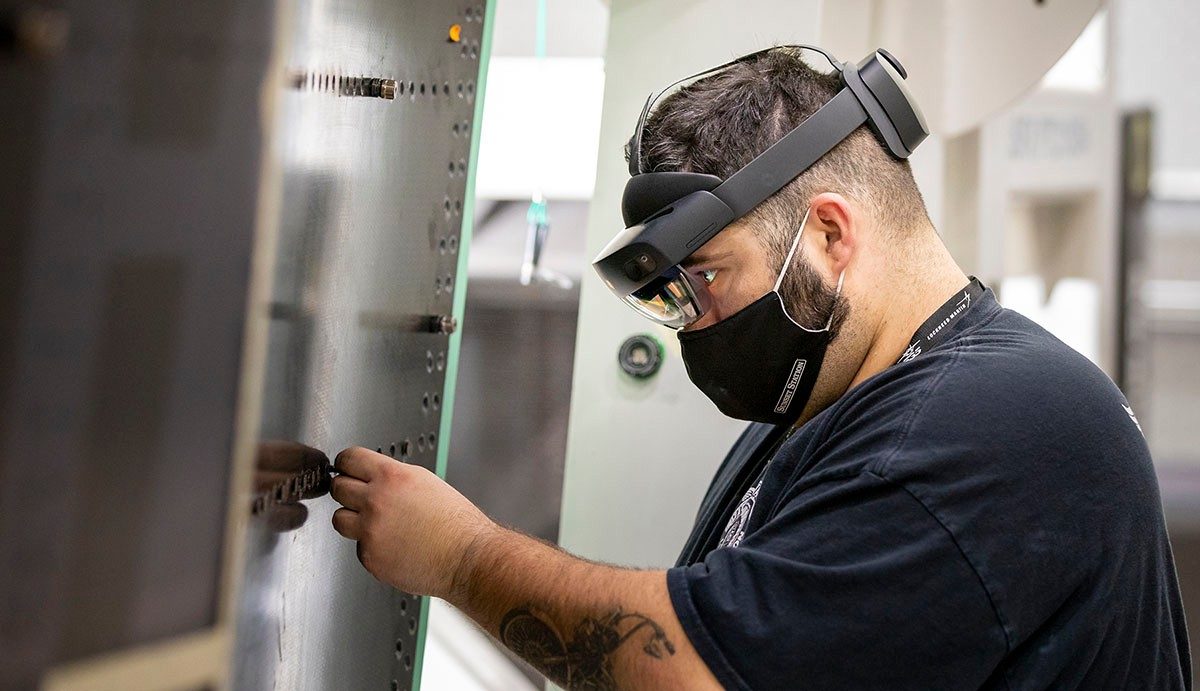
Lockheed Martin is revolutionizing our factories with smart tools, connected machines, networked supply chains and AR/VR for technicians that speed production and improve quality.
Automation-enabling technologies are being used for marking, painting, welding and bonding, whether done by a fully automated machine or paired with a skilled worker. Human-machine collaboration extends to virtual and augmented reality-enabled technologies as well. Tools with these capabilities are becoming increasingly integrated into training, production and quality assurance, the latter of which includes conducting virtual inspections with digital metrology. Similarly, smart tools are used for electronic harness boards, factory-wide simulation projects and solar arrays for satellites, among other things. Smart tools include all devices or systems that are portable, digital, networkable and able to upload to a data repository; traceable to a calibration recall system; and capable of measuring a specific attribute, feature or process. Accordingly, Lockheed Martin’s investments into these tools are far-reaching and have the potential to yield exponential returns.
Bringing the Digital Thread to Life
Digital factory investments are a critical element of Lockheed Martin’s Mission-Driven Transformation, enabling a continuous digital thread from product design all the way through to production and sustainment.
“We start to see the digital thread come to life in our factories,” Sarpu said, “but digital engineering brings manufacturing expertise into the product life cycle long before we start to bend metal. With digital models, we can simulate factory flow and virtually fabricate, assemble, inspect and test prior to physically building the product. And with digital factory capabilities, those same threads are used to build model-based work instructions, power mixed-reality applications and program smart tools.”
In addition to generating higher-quality hardware output and flattening first-article learning curves, digital factories are using the digital thread to deliver products’ as-built digital twins. Customers can use these digital twins to inform sustainment planning.
Although the technology is complex, the goal is simple: Transform with urgency to deliver the speed, agility and insights our customers need to stay ahead of rapidly evolving threats.